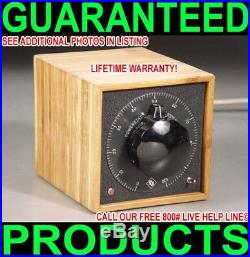
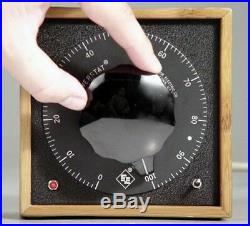
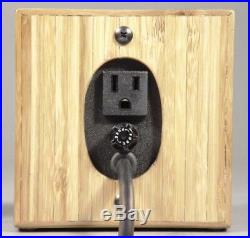
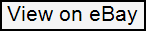
VARIAC SPEED VOLTAGE CONTROL VINTAGE DIEHL CROCKER EMERSON ANTIQUE ELECTRIC FAN. PLEASE LOOK AT ALL OF THE PHOTOS AND TEXT FOR ADDITIONAL INFORMATION, AND TEL. ME IF YOU NEED ADDITIONAL INFORMATION. THIS IS A BRAND-NEW, TOP QUALITY. THAT HAS BEEN CUSTOM MADE, NOT A POORLY MADE COPY FROM CHINA! WE ONLY SELL THE VERY HIGHEST QUALITY VARIACS FROM U. COMPANIES THAT ARE BUILT TO LAST A LIFETIME! WE OPERATE A FACILITY THAT EXPERTLY CUSTOM BUILDS THESE VARIAC TYPE AUTOFORMERS. AFTER CAREFUL ASSEMBLY, EVERY VARIAC IS FULLY TESTED AT THE MAXIMUM RATED LOAD IN OUR FULLY EQUIPPED TEST LAB! THIS IS A CUSTOM BUILT BENCH VARIAC OF THE TYPE THAT HAS BEEN USED BY ENGINEERS AND TECHNICIANS TO DESIGN AND REPAIR ELECTRONIC EQUIPMENT FOR THE LAST 50 YEARS! IN ADDITION THIS VARIAC IS IDEAL FOR POWERING OLDER TUBE AUDIO EQUIPMENT THAT REQUIRES SLOW AND CAREFUL INITIAL TURN ON TO PREVENT DAMAGE TO OLD TUBE FILAMENTS AND “FORM” ELECTROLYTIC FILTER CAPACITORS, AND ALSO OPERATE OLDER EQUIPMENT THAT ORIGINALLY WAS DESIGNED FOR 110/115 VOLT OPERATION (NOT THE 120-VOLTS WE HAVE TODAY). THIS VARIABLE AC POWER SOURCE FEATURES A BEAUTIFUL HARDWOOD CASE MADE FROM SOLID BAMBOO! YOU ARE NOT LIMITED IN POWERING MULTIPLE PIECES OF EQUIPMENT BECAUSE THERE IS ONLY ONE OUTLET ON THE VARIAC, BY SIMPLY CONNECTING A STANDARD MULTIPLE OUTLET POWER STRIP TO THE VARIAC OUTPUT, SEVERAL DEVICES CAN BE CONNECTED AND PROTECTED AT THE SAME TIME AS LONG AS THE TOTAL LOAD DOES NOT EXCEED 5-AMPS. THIS UNIT HAS BEEN COMPLETELY TESTED IN OUR FULLY EQUIPPED LAB AND IS GUARANTEED TO BE WORKING AND MEETING ORIGINAL FACTORY SPECIFICATIONS. PLEASE CALL THE DAVID RIDDLE CO. DRCO 10AW, VARIABLE AUTO-TRANSFORMER (VARIAC) B12-1019-113-W. The following is the step-by-step process by which I fully restore both metered and non-metered variable autotransformers (“variacs”) into better-than-new condition. I perform a full initial evaluation including a “triage” test for operation of all controls and output range for volts and amps, meter functions plus a 1,200-volts AC “HI-POT” chassis leakage test. I completely disassemble the entire unit and do a full inspection of all components. All hardware and fasteners variac assembly, screws, nuts, switch, power cord, wiring, receptacle, handle, knob, meters, dial plate, nameplate, etc. Are separated and stored for individual and unique processing. Two-prong plugs and receptacles are replaced with new three-prong types all wire, metals, etc. Not used in the final product are recycled. The autotransformer (variac) is fully disassembled into its individual component parts coil w/terminal plate, rotor, brush assembly, shaft, base-plate, etc. And the coil and “brush track” are cleaned and inspected. 4, If the brush track has surface damage, it is “wet hand-lapped” with various grades of abrasives (course to ultra-fine, 150, 220, 400, 600 grit) until it is absolutely flat and smooth and is then heavily electroplated with a silver alloy for high electrical conductivity and to resist oxidation. After the lapping and silver-plating process is completed, the coil assembly is thoroughly washed with detergent and hot water to remove any remaining silver-plating solution. The coil assembly is then baked in a custom-made convection oven at 200°F for two hours to completely remove all moisture and then is allowed to cool. The brass or copper “rotating electrical contact” of the rotor. High-temperature, non-spreading synthetic grease is applied to the sliding bearing surfaces not to the carbon tip! The brush assembly is precisely attached to the rotor and checked for full freedom and ease of movement. All of the other variac components are cleaned and inspected or replaced with new components. The various components of the variac are then carefully reassembled along with the rotating control shaft that has been lubricated with the same synthetic grease. After the variac is fully assembled, a piece of 400-grit sandpaper is placed between the carbon brush tip and the brush-track with the abrasive face touching the carbon tip. While holding the sandpaper, the rotor is rotated back and forth over the sandpaper several times to “bed” the carbon tip to the brush track. While the carbon brush tip is being illuminated with a strong backlight, the rotor is turned through its full sweep observing that no light is leaking between the carbon tip and the brush track. This ensures that the carbon brush tip is in intimate physical and hence electrical contact with the brush track at all times. Any interruption of the intimate contact of the carbon brush tip and the coil brush track surface while under electrical load will cause instant and irreparable catastrophic “arcing” damage to the brush-track. All of the sheet metal or cast housings and case components covers, “shields”, dial-plate, mounting plate, etc. Are washed with degreaser, thoroughly rinsed with hot water and oven dried. Any of the painted case components that are to be re-painted are stripped using epoxy stripper, washed with detergent, thoroughly rinsed with hot water and oven dried. Prior to being repainted, the sheet metal components, are examined for defects dents, bends, deep scratches, holes, flatness, trueness, etc. And several custom made tools: “picks”, “dollies”, metal, wood and plastic “forms”, etc. Plus various hammers and files, are utilized for “pick-and-filing”-type “repousse”, hammering out dents and scratches from the inside and filing back the expanded metal to the original desired form or shape. Any unwanted holes are filled with a custom-machined metal (aluminum or steel) “plug” that is inserted into the hole that has been “chamfered” front and rear. The plug is then secured with a 2-ton pneumatic rivet squeezer, fitted with polished anvils, that flows the metal plug, filling the hole. Excess metal is carefully filed or sanded flush to the metal surface providing an invisible and permanent repair when painted. All bare-metal surfaces to be painted are fully sanded with various grits of aluminum oxide and/or silicon carbide (carborundum) sandpapers to provide a “tooth” on the metal surface, greatly improving the adhesion of the applied paint finish. In addition, all sharp metal edges are “radiused” to prevent the paint from “creeping” away from the edges due to “surface-tension” effects. All painted surfaces are “baked” or “cured” in a 200°F convection oven for a minimum of two hours ensuring a well adhered, durable and beautiful finish. Depending on the condition and the specific type of the variac’s circular metal dial plate and model/type/specification nameplate (“litho” printed, “silk-screened” or “etched” with paint fill), various methods are utilized in restoring these components. Before restoring any of these components, these parts must be washed with detergent, thoroughly rinsed with hot water and oven dried. Litho-printed plates, if possible, are generally touched up by hand using various small brushes and custom-mixed paints, and are carefully painted while protecting the printed nomenclature from being painted over. If the nameplate is large and the damage includes large areas of missing ink or paint, all of the nomenclature letters, numbers graphic entities, etc. Are covered with masking tape. I use a brand-new, special, long, thin razor blade and an “Exacto” knife, to carefully cut away the masking tape around all of the nomenclature and then the remaining masking tape is “stripped” away. The masked plate is then spray-painted with the proper background color (usually semi-flat black). Immediately after painting, I use extreme care, and the sharp tip of the Exacto knife to “prick” up the edge of the various pieces of masking tape and use a pair of tweezers to carefully peel off the tape while not allowing anything to touch the drying paint during removal. This process of removing the masking tape while the paint is still wet allows the paint to flow slightly and smooth out the sharp paint line edge resulting from the masking tape. Etched and paint-filled type dial and nameplates are first evaluated through “wet mild abrasion” using #3/0 stainless-steel wool and water to remove oxidation from the “raised” nomenclature and borders and loosening any fill paint not well adhered. If the fill paint is irregular in surface finish or is missing in spots, the plate needs to be fully stripped with epoxy stripper, washed with detergent, thoroughly rinsed with hot water and oven dried. The proper color and type of fill paint (lacquer works best) is applied in several layers or coats to build in thickness up to, or just below, the level of the raised nomenclature while allowing each layer to dry for several minutes between coats. After the fill painting is complete, the plate is baked in a 200°F convection oven for a minimum of one hour. Depending on the etched plate’s substrate material, aluminum, brass or nickel-plated brass, different processes apply. For aluminum and brass plates (or where the nickel plating on the brass has eroded), a metal sanding block (2.5″L X 1″W X 1/4″ H) wrapped in 400 grade wet-or-dry sandpaper is utilized to “wet sand the plate in a circular motion. Under cold running water. I carefully observe each portion of the plate being sanded and note when the raised portions of the nomenclature begin to appear through the fill paint. When the raised nomenclature in the spot being sanded has fully appeared (letters / graphics appear without breaks), I stop sanding in the original spot and move to the next area of the plate until all of the nomenclature has been revealed through the fill paint. If small areas of the plate are missing fill paint after sanding, it can be carefully hand touched-up with a small brush to correct any defects. For nickel-plated brass plates, I use #1 stainless-steel wool and running water to remove the unwanted fill paint. This process takes much longer to reveal all of the nomenclature and requires careful attention not to cut through the fill paint no sanding block, only your finger! , but the stainless-steel wool will not scratch the nickel plating; sandpaper will cut through the thin plating almost immediately! The finishing process for all of the plate types is the same-a clear lacquer seal coat. Unfortunately, a glossy finish will clearly reveal all of the touch-up work! To eliminate this problem, a textured, clear lacquer finish provides the answer but typically available matte finishes are not sufficiently textured to hide even minor surface defects. The first step in the texturing process is to place the plate in a 200°F convection oven for a minimum of ten minutes to reach full temperature evenly across the whole plate. The heated plate is removed from the oven and immediately placed on a spinning (30-40rpm) painting “turntable” while the clear lacquer sprayer (or can) is held at least 24-inches above the plate allowing the fine mist of droplets to land evenly (because of the rotation) across the entire plate’s surface. This process is most evenly and easily accomplished if a large light source the sun? Is reflected off of the plate’s surface at an “oblique” or sideways angle. The fine lacquer droplets will be partially drying as they fall to the plate and then the heated plate will “freeze” them into a uniform and highly textured finish. When the finish is not even or is not textured enough, the plate can be re-heated and re-sprayed for the desired textural effect. Test “coupons” or sample plates are tried first! When the variac is equipped with a single-or multiple-analog meters, these will need to be individually cleaned and calibrated. Depending on the age of the particular variac, these analog meters are either housed in “thermosetting” bakelite cases with glass “windows” or “thermo-plastic” cases with painted and clear plastic “window covers”. The bakelite cased meters typically use screws to hold the two-part cases together. Meters with thermo-plastic cases are typically held together with “snap-on” front covers that must be carefully pried apart very carefully so as not to crack the “styrene” type plastic that becomes even more fragile as it ages. In either case, great care must be exercised during and after disassembly to prevent damage to the ultra-delicate internal meter components needle, scale, hair-spring, wiring, coils, etc. ; one inadvertent hand movement or finger touch to these components can render the entire meter irreparable! The front cover is washed inside and out using warm water and dish soap and a soft bristled brush to get in the corners and completely rinsed in warm water. The cover is then carefully dried with a “just-laundered” and tumble-dried (without softener sheets) plush cotton towel while using a strong “back light” to confirm there are no streaks in the window area and great care is needed not to snag the tiny and fragile “zero-adjust” pin that resides in the cover. Unlike meters with glass windows, thermo-plastic covers have windows that are very susceptible to surface scratching and must be carefully polished to eliminate this highly visible and distracting defect. Very minor and fine superficial scratches can generally be removed by hand with a commercially available, mildly abrasive, plastic polish and a clean soft cotton cloth. With deeper and more serious scratches, a multi-step process is usually required. Depending on the meter cover configuration, masking of the painted areas of the cover may be needed to prevent damage during this process. The window area is first “wet hand-sanded” with various grades of abrasives (course to ultra-fine, 150, 220, 400, 600 grit) until all of the visible scratches have been eliminated and the window appears upon inspection with a back light to have a even matte, translucent appearance. While using a soft flannel polishing wheel, rotating at the proper speed and with the appropriate “polishing-compounds” for styrene thermo-plastics, I carefully polish the meter cover window to a crystal-clear, transparent appearance, free of directional polishing marks. This entire process must be monitored visually while using a light touch and continuous movement to prevent permanent and irreversible damage caused by overheating and melting of the fragile plastic material. After polishing, the meter cover is again washed to remove any residual polishing compound and dried. Thermo-plastic meter covers have a strong tendency to acquire and hold a static electricity charge, and this charge can “lock” or move the sensitive meter needle up or down scale rendering the meter inoperative. To continually drain off this static charge, a very thin and transparent coating of clear liquid dish detergent is applied to all of the inside surfaces of the meter cover. I use a cotton “Q-tip” to spread a tiny amount of detergent evenly inside the cover and then additional clean and dry Q-tips to polish the soap-film to invisibility. This thin film of detergent is “ionic” and “hygroscopic” and absorbs moisture from the air forming a conductive path to discharge any acquired static charge. The front and rear meter case components when assembled are designed to form a “dust-tight” seal to prevent environmental contamination. If these components have been damaged to the point of allowing dirt and dust to enter, the damaged front or rear cover, or both, must be replaced. If only the front cover is replaced, the rear cover and the meter mechanism must be disassembled and thoroughly cleaned to prevent re-contamination after final assembly. During this disassembly and cleaning process, the meter mechanism is extremely vulnerable to damage and must be secured in a protected location while cleaning the rear cover. In addition, the meter mechanism itself will often be contaminated and must be meticulously disassembled and cleaned under magnification as. This work requires special tools and the “hand” and skill of a watchmaker! Since the meters used in variacs are measuring AC voltages and amps or watts, the specific type of meters most commonly used are of the “iron-vane” design and as such are susceptible to erroneous readings from external magnetic fields, the exact magnetic fields produced by the variac itself! To prevent these external magnetic fields from affecting the accuracy of the meters, thick-steel “shield cups” cover the rear meter covers. After the previous steps have been completed and the meter mechanism, scale and shield cup are all in place, the calibration process can begin. The first step is “balancing the tree” (the moving meter components): the needle, damper vane and the three counter-weights. The meter is placed in an exact horizontal position with the scale facing up and the zero-adjust lever is moved until the needle is set precisely to zero on the scale. When the meter is zeroed, the zero-adjust lever should reside very close to the center of its travel. If it is not, the lever is centered and a fine needle is used to very slightly bend the hair-spring where it attaches to the zero-lever in the appropriate direction to achieve a zero reading. If this bending method causes too much deflection of the hairspring from its concentric position around the pivot, the length of the hairspring must be altered very slightly by un-soldering it from the zero-lever and re-soldering at the correct position. The meter is raised from the horizontal to an upright vertical position with the scale facing front and the scale nomenclature positioned horizontally left to right. The needle should remain at the zero position; if it changes to below or above zero, the direction and amount is noted. While the meter remains vertical, the meter is rotated 90 degrees clockwise, and the needle position is noted. The meter is then rotated 180 degrees counter-clockwise, again the needle position is noted. Depending on the outcome of these tests, each of the three counterweights (bottom-main, left and right) attached to the tree are all adjusted individually in the appropriate direction along each weights “arm” of the tree until the meter needle remains at zero position in all of the above positions to within one half of one “minor division” of the scale. Since all of the three counter-weights interact with each other during the tree-balance adjustment process, the meter must be continually rotated along the various axes while adjusting the three weights. The electrical calibration of analog iron-vane AC meters requires a precision calibrated source of volts and amps accurate to at least 0.1% over the entire range of the meters to be tested. The “calibrator” is electrically connected to the meter under test and the meter is precisely zeroed in the axial position it will usually reside in during use. Noting the reading at full-scale, the calibrator is then adjusted to the first “major-division” above zero and the reading noted. If both readings are low or both high in the same amount, a course deflection adjustment is made. Depending on the type and brand of the specific iron-vane meter, this adjustment is made either by loosening the lock-screw of the deflection paddle and shifting it’s position in the “coil cup” and re-locking it. On some meters this is accomplished by actually bending the paddle’s position using a small screwdriver. If the screwdriver is made of metal, it will have to be moved away from the adjustment area as its presence will effect the needle position substantially. Adjusting the output of the calibrator to the various major/divisions across the meter’s scale will indicate the “linearity” of calibration. If the meter is not linear, there is an additional adjustment point usually to the left of the coarse adjustment point that is utilized to calibrate the upper portion of the scale. Both of these calibration points interact with each other so it is necessary to continually change the output of the calibrator to various major-division set points and, in addition, always check the zero set point between tests to confirm it wasn’t bumped during these adjustments. Through the use of both calibration adjustment points the meter should be able to be adjusted to within 2-3% accuracy across the entire scale and very accurate at any selected single point such as 120-volts on a 0-150 voltmeter for use at American voltage standards. After the meters have been cleaned and calibrated they are re-assembled ensuring that there are absolutely no loose dust or dirt particles remaining in the meter case or visible in. Or on the window and that the zero pin is lined up with the zero lever so that the external zero adjustment is working properly. After final re-assembly, the meters are carefully re-checked visually, mechanically and electrically. The variac knob is usually made of bakelite, and as such, is subject to impact damage such as chipping and surface scratches, severe chips cannot be repaired so a chipped knob is replaced. Most scratches can be polished out to a very high sheen. Other knob materials include thermo-plastics that are very susceptible to scratching because the material is soft, and since it is not heat resistant, polishing is fairly difficult and time consuming. The first step in restoring either type of knob is to wash it in hot soapy water using a toothbrush to remove any dirt or finger oil residue. After thoroughly drying the knob, inspect it to determine the severity of the scratches, deep ones will not polish out and need to be wet-sanded first using a sequence of coarse to fine sandpaper (as described previously in the meter cover restoration) until a smooth matte finish is obtained. While using a cotton polishing wheel, rotating at the proper speed and with the appropriate “polishing-compounds” for thermo-setting plastics, the knob is polished to a mirror-like “piano-finish” appearance, free of directional polishing marks. Since bakelite is a high temperature plastic, the polishing process can be fairly aggressive. When polishing a thermo-plastic knob, the entire process must be monitored visually while using a light touch and continuous movement to prevent permanent and irreversible damage caused by overheating and melting of the fragile plastic material. After polishing the knob it is again washed to remove any residual polishing compound and then dried. The final step in the knob restoration is to “re-fill” the molded in “cursor” or “pointer” markings with paint. When any residual paint remains in the cursor areas, it must be completely removed before re-filling. The paint used for this application is a “thinned” white, gloss enamel, obtained from a can of spray paint dispensed into a cup. A long, very thin, camel’s hair brush, fully filled with paint, is tipped into the cursor recess allowing the paint to flow through “capillary” action to fully fill the recess. When paint flows outside of the cursor recess, a heat gun is used to partially dry the surface of the paint, and a thin plastic card or fingernail is used to scrape-away any excess paint from the knob surface around the cursor recess. If the variac includes a “u-shaped” aluminum carrying handle, it is first placed on its side on a flat surface to determine if it is twisted by pushing on each of the tips and determining if it is “rocking” and not perfectly flat. The handle is then “trued” by manually bending or twisting the handle and repeatedly checking to confirm flatness. The two tips of the handle are “radius” sanded on a belt sender to remove any original fabrication “shearing” marks as these will be clearly visible when the handle is folded to the back of the variac when it is in use. An abrasive “scotch wheel” on a rotating arbor is used to evenly “grain” the aluminum handle along it’s length on all surfaces. Soap-filled steel-wool is used in a “stroking” linear fashion along the length of the handle to. Produce a bright lustrous finish. The handle is then washed to remove any residue and dried. All “nickel-plated” screws, bolts, nuts, washers etc. Are “brightened” by removing the nickel-oxide from their surfaces by submerging them in muriatic “pool acid” for ten minutes and then thoroughly rinsing and “agitating” them in continuously running hot water for a minimum of two minutes. This hardware is dried with a soft cotton towel. Zinc, cadmium and chrome plated parts are manually restored using hand or powered. Wire brushes and steel-wool as these parts cannot be “acid washed”. The power cord brass plug-tips are brightened with sandpaper and soap-filled steel-wool. The power cord plug and jacket is first washed with detergent / degreaser and hot water to remove water- soluble dirt and residue and then thoroughly dried. A lacquer thinner soaked rag is used all along the cord length and plug surfaces to remove any hand oils or sticker tape residue. The power cord and all internal wiring that will be soldered during final assembly is “prepped” by trimming all wire ends and stripping off an appropriate amount of insulation, twisting the stranded ends and then individually “tinning” each wire end with “63/37 tin/lead alloy, rosin-core solder”. The tinned wire ends are formed into hooks with “needle-nose” pliers for insertion into the various solder tabs and terminal holes of the interconnected internal components. Variac dial plates and name-plates are re-attached to the case components with aluminum rivets, brass eyelets or stainless steel “drive-screws”. Raised cast-in nomenclature numbers and letters are hand filed or machine/milled to reveal the contrasting aluminum through the painted surface to enhance readability. Power cords are secured and “strain relieved” with either a “Heyco” insulated feed-through or a rubber grommet and internal cord-clamp. All of the restored components are carefully re-assembled in a specific sequence determined in advance by the ease, accuracy and cosmetic protection required for each element or assembly. New, properly-rated fuse holders are installed and all internal wiring that will be soldered, is secured mechanically prior to soldering. All connections made with “solderless, crimp connectors” are attached to wire ends with a “ratchet” type crimper fitted with the proper “die” for the individual connector type and size. During re-assembly, all “self-tapping” machine screws and sheet metal screws are discarded and replaced with either nickel-plated or stainless-steel machine screws. All threaded holes in castings are “re-tapped” with the appropriate machine tap using a custom-made power tapping tool. All sheet metal holes that originally accepted sheet-metal screws are drilled to a specific diameter to accept “pressed-in, pre-installed nuts” for machine screw fasteners. Any fasteners that are able to have their phillips “cross-point” or “straight-slot” screwdriver points and “hex nut-flats” aligned in a uniform pattern are so aligned for a pleasing cosmetic effect. The polished variac knob is the last component installed to protect it’s cosmetic appearance. The knob is carefully aligned to match dial-plate markings and is securely fastened to the variac operating shaft. After final assembly has been completed, and the overall cosmetic inspection has been completed, the properly rated fuses are installed, the power switch is placed in the “on” position, the knob is positioned mid-scale and the power cord is plugged into a “hi-pot”, high-voltage (1,200vac) test source. The high voltage is applied between both “hot” and “neutral” power cord pins and the variac chassis for a one-minute insulation test. After the variac has successfully passed the high-voltage insulation test, the power cord is plugged into a specially-configured metered variac that is brought up slowly to the full rated input voltage of variac under test, and the “quiescent” or no-load excitation current is measured as the variac knob is rotated through it’s entire range. The variac knob is rotated fully counter-clockwise and the test variac’s output is connected to a precision “instrumented” load that is configured to provide a zero to full load to the test variac. If the variac under test is metered, the meters will again be checked at several test voltages and currents to confirm that they meet the calibration specifications. The last restoration step is affixing a DRCO label printed with a toll-free telephone number to the rear or bottom of the variac confirming that the previously described restoration process has been completed and the variac is now guaranteed for life! All company and product registered trademarks are acknowledged and are the property of their respective companies. Please be sure to read all text COMPLETELY for IMPORTANT information, specific to this item. If you have any additional questions about our terms and conditions of sale please give us a call. Note: All manufacturers names and models are used for illustrative purposes only. AND MAY NOT BE USED FOR ANY PURPOSE WITHOUT WRITTEN PERMISION. Powered by SixBit’s eCommerce Solution. The item “VARIAC SPEED VOLTAGE CONTROL VINTAGE DIEHL CROCKER EMERSON ANTIQUE ELECTRIC FAN” is in sale since Tuesday, August 8, 2017. This item is in the category “Consumer Electronics\Vintage Electronics\Vintage Audio & Video\Vintage Parts & Accessories\Vintage Tubes & Tube Sockets”. The seller is “davidriddle” and is located in Van Nuys, California. This item can be shipped to United States.
- Country/Region of Manufacture: United States
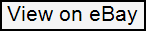